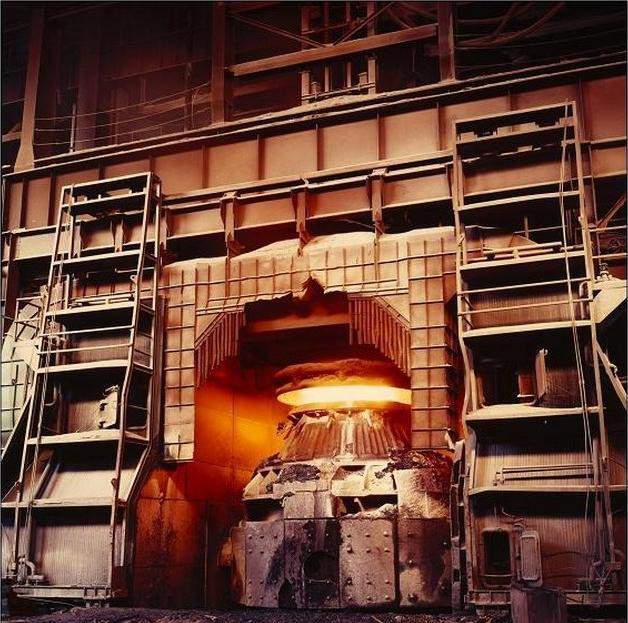
成果简介
转炉钢水冶炼过程中会产生大量含氧化铁粉尘的高温烟气,其主要成分为一
氧化碳,是一种热值较高的工业燃料,如不进行有效回收处理和控制排放,不仅污染大气环境,还会造成能源浪费。转炉煤气回收是把转炉生产过程中的副产品CO 进行回收再利用的生产工艺,它将高温烟气通过汽化烟道进行冷却、净化处理后,得到可回收的转炉煤气,其经济价值和社会效益不言而喻。
目前国内炼钢企业的转炉煤气回收系统由于部分技术装备及控制方法比较落后,煤气回收和烟气减排效果差。本项目采用滑模变结构控制技术,实现烟气流量的自动调节,从而将炉口烟气压力控制在微差压范围内,有效地避免烟气外溢或向罩内吸入空气,达到较好的控制烟气排放和煤气回收效果。由此避免大量的 CO 复燃和冶炼过程的涌浪,稳定钢水冶炼过程, 从而在吹炼终点时尽可能达到目标钢水的碳含量和温度,提高吹炼命中率,缩短冶
炼周期,降低消耗。在此基础上,本项目又提出了一种基于提高 CO 浓度的优化控制方案,利用模糊 RBF 神经网络在线辨识出炉口压差与 CO 浓度之间的数学模型,根据辨识模型实时调整压差控制回路的设定值,并通过系统跟踪控制,将炉口压差控制在该设定值附近,从而达到显著提高 CO 浓度和煤气回收质量的效果。
成熟程度和所需建设条件
本项目先后成功应用于马钢和宝钢梅山炼钢厂 50 吨和 150 吨转炉,结果表明节能减排和煤气资源回收效果显著,经济和社会效益明显。
技术指标
应用该技术使马钢 50 吨转炉的煤气回收水平提高了大约 17%, 即由原来平均 90m3/t 提高到目前平均值 103 m3/t,煤气热值由原来平均 1450kCal/m3 提高到目前平均值 1680 kCal/m3,在梅钢 150 吨转炉的实施使转炉煤气回收水平提高了大约 20%,即由原来平均 90m3/t 提高到目前平均值 107 m3/t,煤气热值由原来平均 1610 kCal/m3 提高到目前平均值 1780 kCal/m3,节能降耗效益显著。
市场分析和应用前景
本项目成功地将系统建模、滑模变结构及过程优化控制技术集成应用于转炉煤气回收系统,有效地解决了模型在线辨识、炉口压力调节、CO 浓度及煤气热值提高等关键技术问题,在集成创新和工程应用方面达到了先进水平。该项目研究成果具有自主知识产权,可形成转炉煤气回收系统智能优化控制的国产化技术,具有较好的推广价值和应用前景,可为国内同行业使用和借鉴。
社会经济效益分析
项目实施以来,由于煤气回收效率的提高,使得烟气排放量也有所降低。在转炉实施吹氧、加料、降罩等工艺操作过程中,炉口喷火现象明显减轻,系统运行平稳,由于回收煤气量明显增加,也有效地减少了向大气中排放的烟气量,不仅为企业带来可观的经济效益,也有效地保护了环境,产生了良好的社会效益。